Centrifugal Pump Advantages and Disadvantages
- Sam Snodgrass
- Dec 10, 2024
- 3 min read
Centrifugal pumps are one of the most commonly used pumps in various industries due to their simplicity, reliability, and ease of use. However, like any other machine, centrifugal pumps have their advantages and disadvantages. In this article, we will discuss the benefits and drawbacks of using a centrifugal pump.
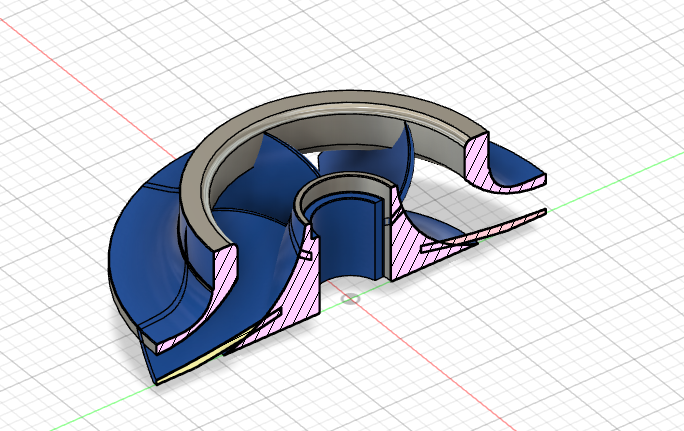
Introduction
Centrifugal pumps are mechanical devices that are used to transfer fluids from one location to another. They work on the principle of centrifugal force, which is generated when an impeller rotates inside a casing. As the impeller spins, it creates a low-pressure zone at its center, which draws fluid into the pump, and then it pushes it outwards into the casing, creating a high-pressure zone. This action allows the fluid to be transported from one location to another.
Advantages of Using a Centrifugal Pump
Simplicity and Ease of Use
One of the biggest advantages of using a centrifugal pump is its simplicity and ease of use. These pumps have a relatively simple design, which makes them easy to install and maintain. They also have few moving parts, which reduces the chances of mechanical failure and makes them more reliable.
High Flow Rate
Centrifugal pumps are designed to handle large volumes of fluids, making them ideal for applications that require a high flow rate. They are also capable of handling fluids with varying viscosities, making them versatile and suitable for a wide range of applications.
Cost-Effective
Centrifugal pumps are relatively inexpensive compared to other types of pumps. They also require less maintenance, which helps to reduce the overall cost of ownership.
Energy Efficient
Centrifugal pumps are generally more energy-efficient than other types of pumps, especially when it comes to applications that require a high flow rate. This is because they require less energy to move the same amount of fluid as other types of pumps.
Disadvantages of Using a Centrifugal Pump
Limited Pressure
One of the biggest disadvantages of using a centrifugal pump is that they are limited in terms of the pressure they can generate. This means that they may not be suitable for applications that require high-pressure pumping.
Not Suitable for Viscous Fluids
While centrifugal pumps are versatile and can handle fluids with varying viscosities, they are not suitable for handling highly viscous fluids. This is because the impeller is not designed to handle fluids that are too thick or sticky.
Prone to Cavitation
Centrifugal pumps are prone to cavitation, which occurs when the pressure at the eye of the impeller falls below the vapor pressure of the fluid being pumped. This can cause damage to the impeller and other components of the pump, reducing its efficiency and reliability.
Requires Adequate NPSHa
Centrifugal pumps require adequate net positive suction head available (NPSHa) to operate efficiently. If the NPSHa is insufficient, the pump may experience cavitation, which can lead to mechanical failure.
Conclusion
In conclusion, centrifugal pumps have both advantages and disadvantages. They are simple, easy to use, cost-effective, and energy-efficient. However, they are limited in terms of the pressure they can generate, not suitable for handling highly viscous fluids, prone to cavitation, and require adequate NPSHa to operate efficiently. It is essential to consider these factors when selecting a centrifugal pump for a particular application.
FAQs
What are the most common applications for centrifugal pumps?
Centrifugal pumps are commonly used in industries such as water and wastewater treatment, chemical processing, food and beverage, and HVAC systems.
Can centrifugal pumps handle abrasive fluids?
Yes, centrifugal pumps can handle abrasive fluids, but it may cause wear and tear on the impeller and other components of the pump.
What is the best way to prevent cavitation in a centrifugal pump?
The best way to prevent cavitation in a centrifugal pump is to ensure that the NPSHa is adequate for the application. This can be achieved by increasing the inlet pressure or lowering the fluid temperature.
Can a centrifugal pump handle fluids with varying viscosities?
Yes, centrifugal pumps are capable of handling fluids with varying viscosities. However, they are not suitable for handling highly viscous fluids.
How does the impeller of a centrifugal pump work?
The impeller of a centrifugal pump rotates inside a casing and creates a low-pressure zone at its center, which draws fluid into the pump. The fluid is then pushed outwards into the casing, creating a high-pressure zone, allowing the fluid to be transported from one location to another.